1、Formulation of Anilox Roller in Aluminum Foil Bag Production,
In the dry lamination process, three sets of anilox rollers are generally required for gluing anilox rollers:
Lines 70-80 are used to produce retort packs with high glue content.
The 100-120 line is used for the packaging of medium-resistant products such as boiled water.
Lines 140-200 are used to produce general packaging products with less gluing.
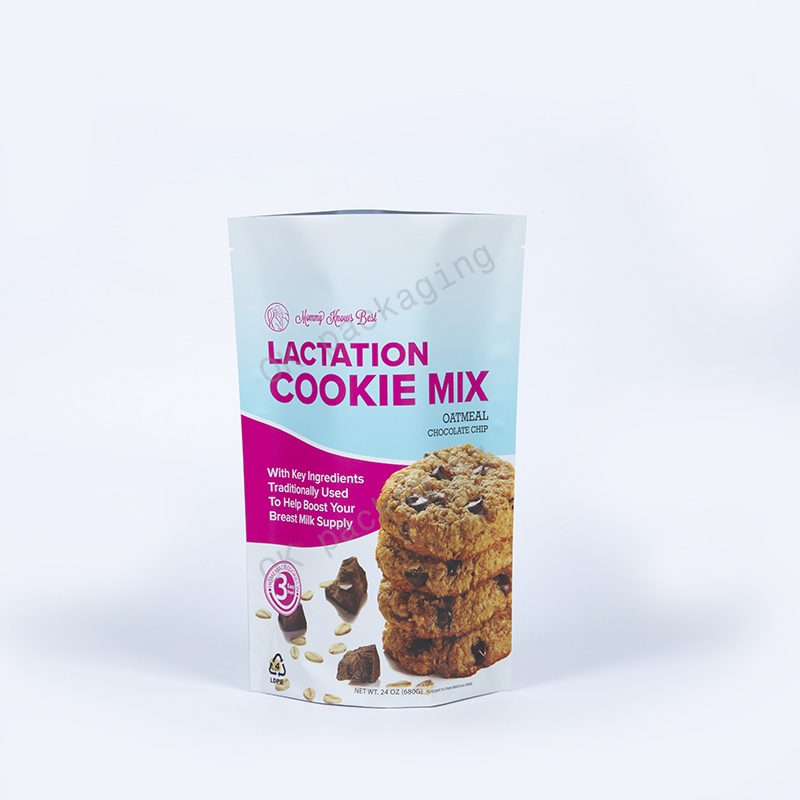
2、Composite key parameters in the production of aluminum foil bags
Oven temperature:50-60℃;60-70℃;70-80℃。
Compound roll temperature:70-90℃。
Compound pressure:The pressure of the composite roller should be increased as much as possible without destroying the plastic film.。
About several specific situations:
(1) When the transparent film is laminated, the temperature of the oven and the laminating roller and the ventilation in the oven (air volume, wind speed) have a great influence on the transparency. When the printing film is PET, the lower temperature is used; when the printing film is BOPP。
(2) When compounding aluminum foil, if the printing film is PET, the temperature of the compounding roller must be higher than 80℃, usually adjusted between 80-90℃. When the printing film is BOPP, the temperature of the compounding roller should not exceed 8
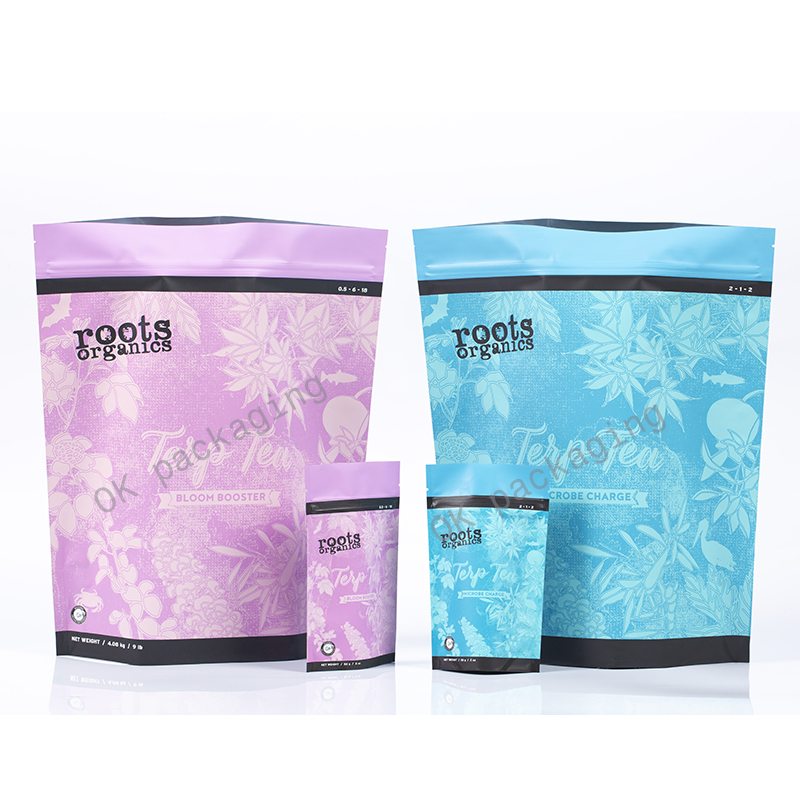
3、Foil bags are cured during production.
(1) curing temperature:45-55℃.
(2) curing time:24-72 hours.
Put the product into the curing chamber at 45-55°C, 24-72 hours, generally two days for full transparent bags, two days for aluminum foil bags, and 72 hours for cooking bags.
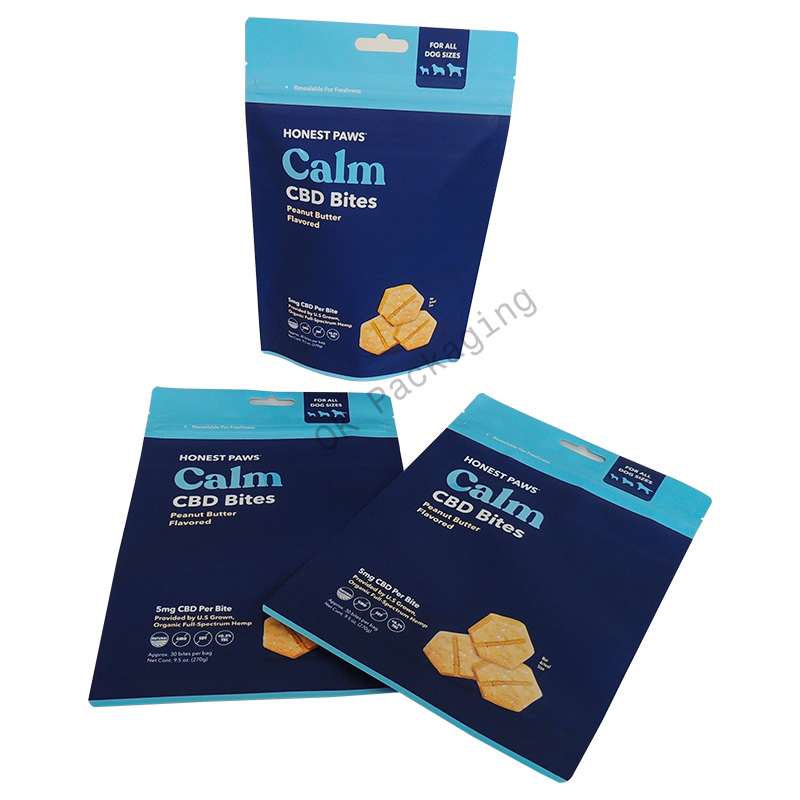
4、The use of residual glue in the production of aluminum foil bags
After diluting the remaining rubber solution twice, seal it, and the next day, go into the new rubber solution as a diluent, when a high product is required, no more than 20% of the total, if conditions are best stored in refrigeration. If the solvent moisture is qualified, the prepared adhesive will be stored for 1-2 days without major change, but since the composite film cannot be judged immediately whether it is qualified or not, the direct use of the remaining glue may cause great losses
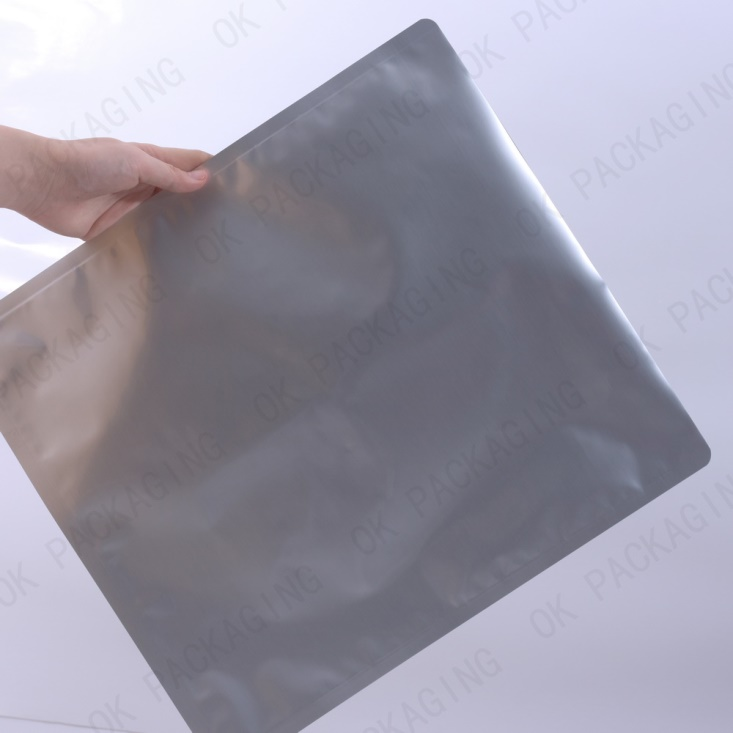
5、Process problems in the production of aluminum foil bags
The inlet temperature of the drying tunnel is too high or there is no temperature gradient, the inlet temperature is too high, and the drying is too fast, so that the solvent on the surface of the glue layer evaporates rapidly, the surface is crusted, and then when the heat penetrates into the glue layer, the solvent gas under the film It breaks through the rubber film to form a ring like a volcanic crater, and circles make the rubber layer opaque.
There is too much dust in the environmental quality, and there is dust after gluing in the electric oven in the warm air, which sticks to the surface of the viscose, and the composite time is sandwiched between 2 base steel plates. Method: The inlet can use a lot of filters to remove the dust from the warm air.
The amount of glue is insufficient, there is a blank space, and there are small air bubbles, causing mottled or opaque. Check the amount of glue to make it sufficient and uniform
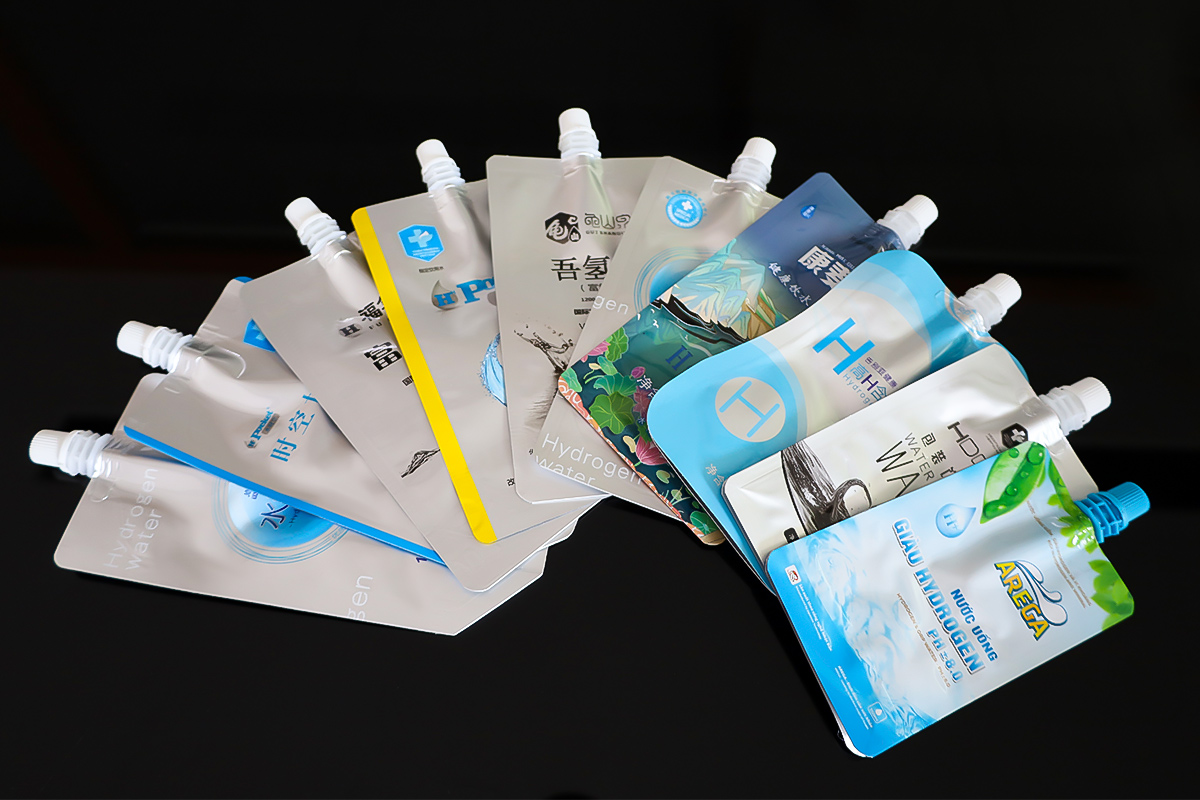
Post time: Jul-18-2022