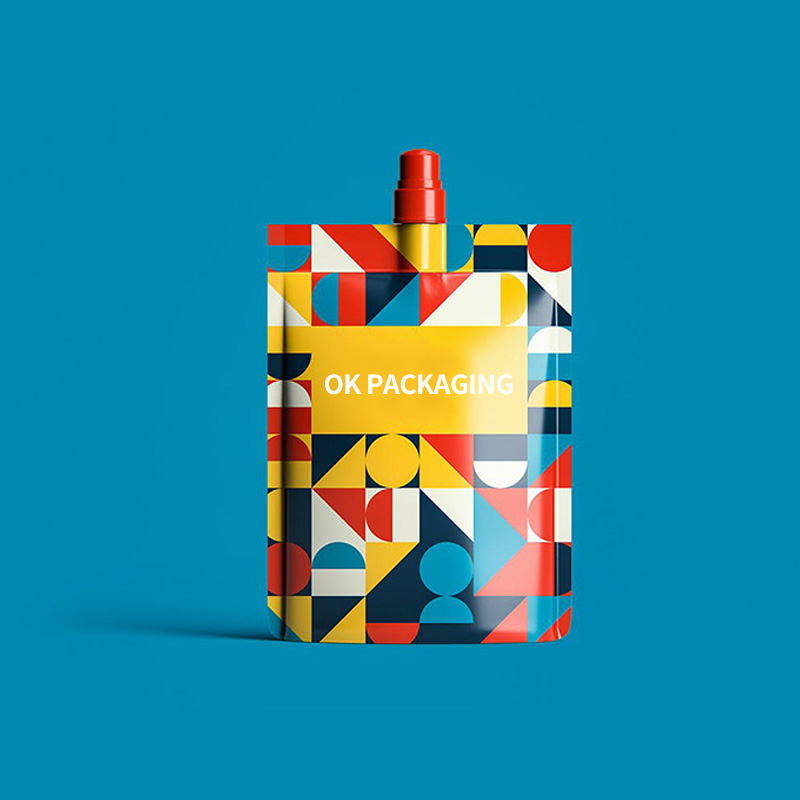
The nozzle packaging bags are mainly classified into two parts: self-supporting nozzle bags and nozzle bags. Their structures adopt different food packaging requirements. Let me introduce to you the bag making process of the nozzle packaging bag.
The first is the heat sealing temperature: the factors to be considered when setting the heat sealing temperature, one is the characteristics of the heat sealing material; the second is the thickness of the film; the third is the number of times of heat sealing and pressing and the size of the heat sealing area. Under normal circumstances, when the same part is pressed many times, the heat sealing temperature can be appropriately set lower. The second is the heat sealing pressure. The timing of heat sealing should also be mastered. The key is the heating method: heating the two heads, so as to determine the quality improvement of the nozzle packaging bag and the symmetry of the bottom sealing.
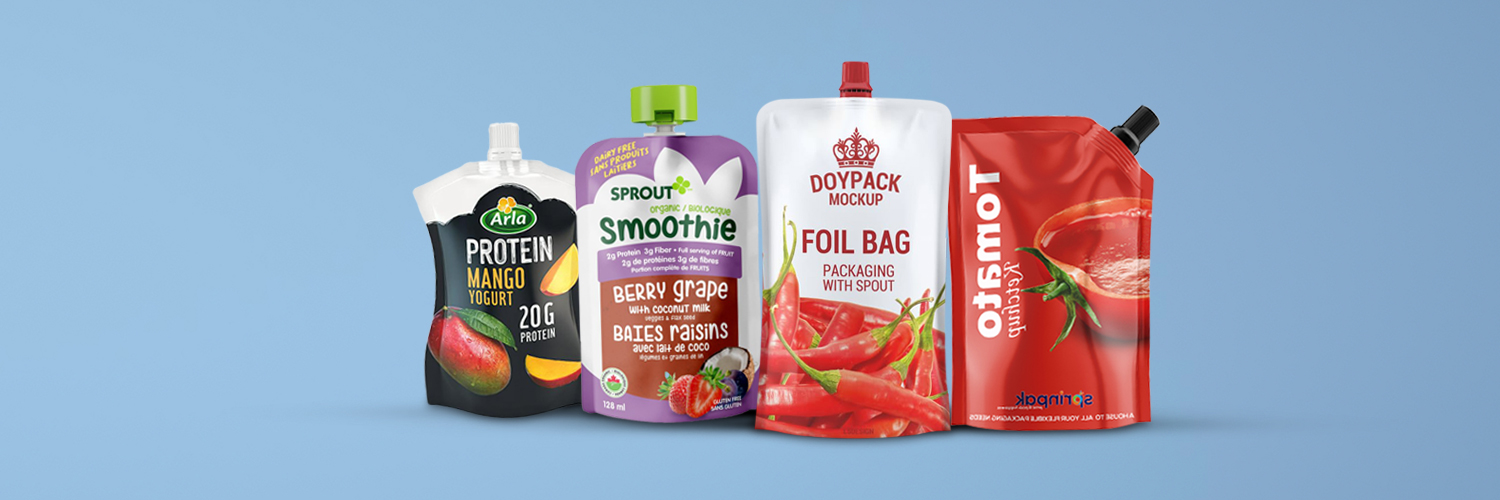
The production of laundry detergent packaging bags is roughly divided into the following steps:
1. Design: This is to design the layout of the packaging bag according to the customer's requirements. A good design layout of the nozzle packaging has a good effect on improving the sales volume of the product.
2. Plate making: It is to make the copper plate required on the plastic packaging printing machine according to the confirmation draft of the nozzle packaging design. This version is a cylinder, and it is a complete set, not a single one. The specific size and number of versions should be determined according to the packaging design in the previous step, and the price is also determined according to the size.
3. Printing: The specific work content on the plastic packaging printing machine is printed according to the first layer of materials confirmed by the customer, and the printed renderings are not much different from the design drawings.
4. Compounding: The so-called compounding is to bond two or more layers of materials together, and stick the ink surface in the middle of the two layers of materials, such as pa (nylon)/pe, where nylon is the first layer of material, that is, the printed material , pe is the second layer of material that is composite material, and in some cases there will be a third and fourth layer of material.
5. Curing: According to different materials and different requirements, different properties are cured in a constant temperature room at different times, so as to achieve more firmness, no delamination, and no peculiar smell.
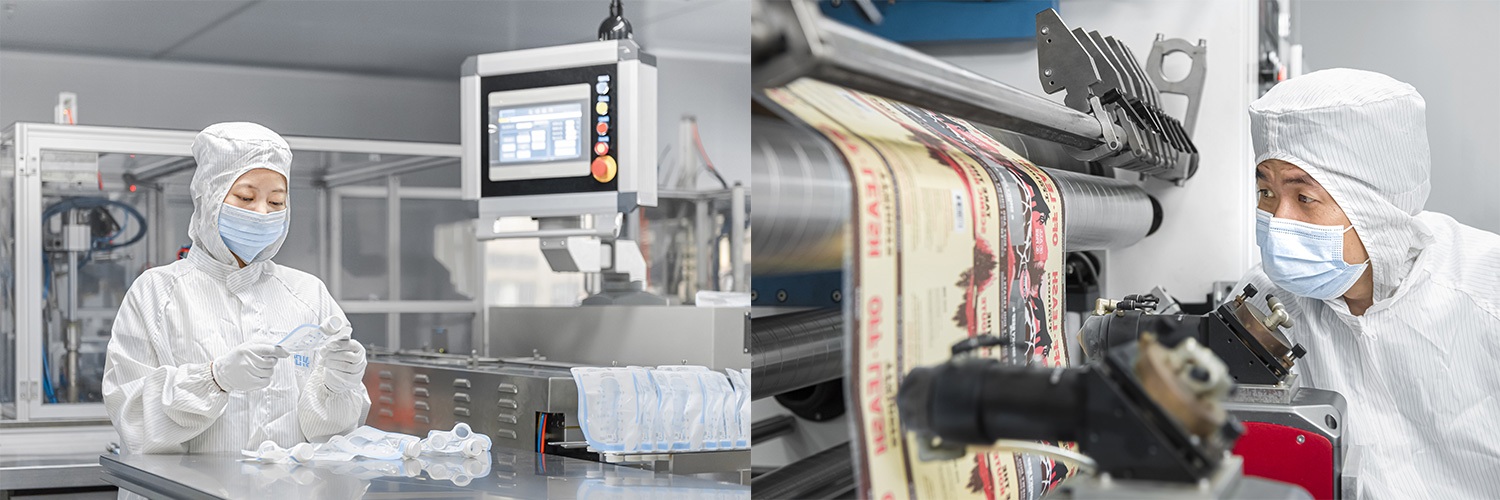
6. Slitting: Slitting is to separate the cured packaging film according to the size requirements.
7. Bag making: bag making is to make the packaging film into finished packaging bags one by one with the corresponding bag making equipment according to the corresponding requirements.
8. Mouth scalding: scalding the mouth is to scald the nozzle on the finished bag.
After the above process is completed, it can be packaged according to customer requirements. However, on the basis of the above, OKpackaging will require the QC department to conduct experimental operations in the standardized laboratory for each item. The next step will only be carried out after each step and each indicator meet the requirements. Deliver satisfactory products to our customers.
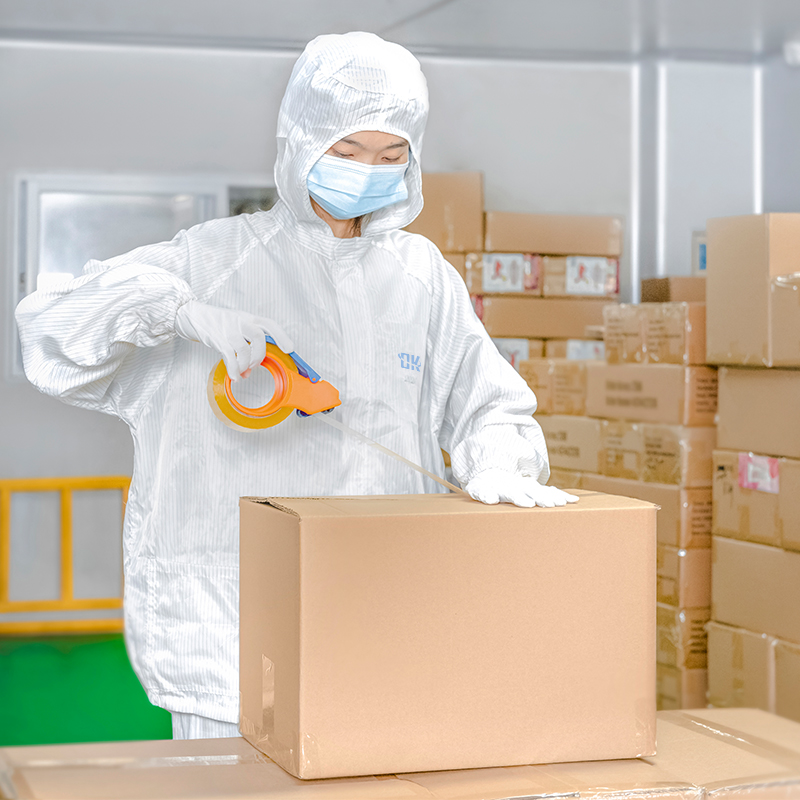
Post time: Aug-03-2022